로스트 폼 캐스팅(Lost Foam Casting)은 폼 패턴과 건식 모래 성형을 결합한 주조 방법을 말합니다. 용융 금속은 원래의 플라스틱 주형이 차지했던 공간을 직접 채우고 대체하며, 냉각 후 필요한 주물을 직접 얻습니다. 폼 패턴은 금속 주조 공정 중에 직접 기화되므로 손실된 폼 주조에는 금형 제거가 필요하지 않습니다. 기껏해야잃어버린 거품 주조 주조소, 일반적으로 사용되는 패턴 재료는 폴리스티렌입니다.
단계잃어버린 폼 캐스팅:
1- 폼 몰드를 사용하여 폼 패턴 및 캐스팅 게이팅 시스템 생성
2- 패턴과 러너를 결합하여 몰드 번들 모듈을 형성합니다.
3- 모듈에 페인트를 담그세요.
4- 페인트 건조
5- 모듈을 모래 상자에 넣고 마른 모래로 채웁니다.
6- 주물을 진동시켜 캐비티를 마른 모래로 채운 후 주물사를 압축합니다.
7- 용융 금속을 부어 폼을 기화시킨 후 원하는 주물을 형성합니다.
8- 주물이 식은 후 주물을 청소합니다. 마른 모래는 재활용할 수 있습니다.
잃어버린 폼 캐스팅의 장점:
1- 로스트 폼 캐스팅은 거의 순 형태 캐스팅 방법입니다. 주조품의 치수 공차는 CT6~CT9에 도달할 수 있으며 표면 거칠기는 Ra=6.3~50μm입니다. 손실된 폼 주물의 모양은 수지 모래 주물과 유사할 수 있습니다.
2- 분실된 거품 주물이 생성할 수 있습니다주물복잡한 모양과 복잡한 구멍이 있습니다. 수지 모래 공정과 비교하여 모래 코어를 더 많이 교체할수록 손실된 폼 주조의 이윤폭이 커집니다. 로스트 폼 캐스팅의 핵심 경쟁력은 엔진 블록, 엔진 헤드, 박스 등 내부 공동이 복잡하고 어려운 주조물을 생산하는 것입니다. 이러한 특성은 로스트 폼 캐스팅의 우수성과 경제성을 최대한 발휘하며, 경량화와 경량화를 실현합니다. 정확한 캐스팅.
3- 손실된 폼 주조에는 금형 제거가 필요하지 않으므로 주조 설계 및 주조 공정에 더 큰 자유가 제공됩니다. 공정 설계 측면에서 로스트 폼 주조 공정은 먼저 부품으로 분할된 다음 전체로 접합된 다음 로스트 폼 공정을 일체형 주조에 사용하므로 로스트 폼 주조는 기존 주조 방식과 경쟁 우위를 갖습니다. 모래 주조.
4- 로스트 폼 주조 공정을 사용하면 노동 강도를 크게 줄이고 고형 폐기물 발생을 줄이며 사용된 건조 모래를 재활용할 수 있습니다. 이 기능은 에너지 절약 및 배출 감소 요구 사항을 충족하며 기존 모래 주조의 혹독한 환경을 변화시켰습니다.
목 | 잃어버린 폼 캐스팅 | 진공 주조 |
적합한 주물 | 엔진 블록, 엔진 커버 등 캐비티가 복잡한 중소형 주물 | 주철 균형추, 주강 액슬 하우징과 같이 구멍이 거의 없거나 전혀 없는 중형 및 대형 주물 |
패턴과 플레이트 | 몰딩으로 만든 폼 패턴 | 흡입 상자가 있는 템플릿 |
샌드박스 | 바닥 또는 5면 배기 | 4면 배기 또는 배기관 포함 |
플라스틱 필름 | 상단 덮개는 플라스틱 필름으로 밀봉되어 있습니다. | 샌드 박스 양쪽 절반의 모든 측면이 플라스틱 필름으로 밀봉되어 있습니다. |
코팅재료 | 두꺼운 코팅이 된 수성 페인트 | 얇은 코팅이 된 알코올 기반 페인트 |
주물사 | 거칠고 건조한 모래 | 고운 마른 모래 |
진동성형 | 3D 진동 | 수직 또는 수평 진동 |
붓는 것 | 네거티브 붓기 | 네거티브 붓기 |
샌드 프로세스 | 음압을 완화하고 상자를 뒤집어 모래를 떨어뜨리면 모래가 재사용됩니다. | 부압을 완화하면 마른 모래가 스크린에 떨어지고 모래가 재활용됩니다. |
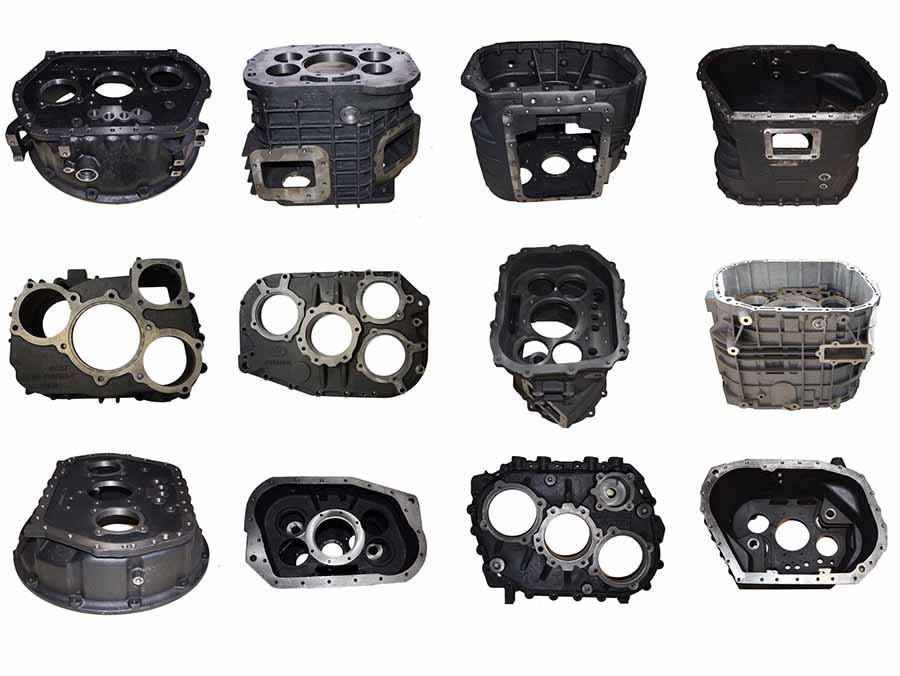